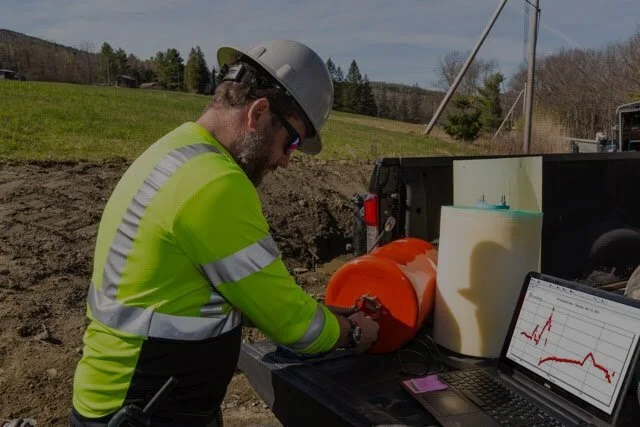
Pipeline Integrity Testing
Each year thousands of pipelines break across all industries, from energy to municipal, causing millions of dollars in damage and downtime. The best way to avoid this problem is to take a proactive approach through pipeline integrity testing. Integrity testing is used to examine the structural integrity of a pipeline system. This type of testing is a universal method that can apply to almost any pipeline.
One of the main types of pipeline integrity testing is hydrostatic testing. Typically, hydrostatic testing is required to install a new pipeline system. Using this type of testing, you can ensure that your new pipeline systems will operate at maximum fitness.
American Pipeline Solutions offers efficient and low-cost pipeline integrity testing solutions to our clients through hydrostatic testing. Keep reading to learn more about our pipeline integrity testing processes, who benefits from it and more.
American Pipeline Solutions’ Pipeline Integrity Testing Process: Hydrostatic Testing
The first step that APS takes when performing hydrostatic testing is to fill your pipeline. Our team uses high flow pumps during this filling process. Once the pipeline has been filled, the pipeline’s pressure is brought to the appropriate pressure level for testing. APS does this by using what is called a “squeeze” pump.
When the pipeline reaches a good line fill, our APS technicians monitor your pipeline’s pressure. This is achieved through the use of monitoring equipment, including calibrated deadweights, digital gauges and recorders.
After testing has been completed to industry standards, APS begins the process of depressurizing your pipelines. The depressuring process is carefully done to ensure the safety of the pipeline. In addition, this process is necessary to maintain compliance with industry code and standards.
What is Pipeline Integrity Testing?
Pipeline integrity testing refers to various processes, hydrostatic testing, used to test the structural integrity of a pipe.
Hydrostatic testing is used to test certain pressure vessels, such as plumbing systems or pipelines. This test aims to examine the strength of a vessel, which is a pipeline in this context. Through hydrostatic testing, you can determine the overall operational fitness of your pipeline. In addition, hydrostatic testing allows you to identify leaks in your pipeline. Because of this leak detection capability, hydrostatic testing is an important process to utilize when testing your pipes.
One scenario where hydrostatic testing is necessary is when you install a new pipeline. Once you’ve installed a new pipeline, you are sometimes required to undergo hydrostatic testing to test your pipe’s integrity.
When it comes to the testing of existing pipelines, integrity testing is required for certain asset owners. Let’s say you’re the owner of a natural gas company, and you transport your gas through pipeline systems. In this scenario, you would be required to test your pipelines every 3-5 years. The frequency of this testing depends on where your pipes are located.
What Pipelines Can be Tested?
Pipeline integrity testing can be performed in any type of pipeline. Examples of these types of pipelines include:
PVC
Cast iron
Ductile iron
PVC
Steel
HDPE
APS has experience performing integrity testing in numerous types of pipeline systems. These pipeline systems include:
New gas pipeline systems
New water pipeline systems
Natural gas pipelines
Water or wastewater lines
This is by no means an exhaustive list. Customers are welcome to contact the APS team to find an appropriate integrity testing solution for their pipelines.
Want to learn how pipeline integrity testing can benefit your pipeline systems?
Contact the team at American Pipeline Solutions today to find the best solution for your needs.