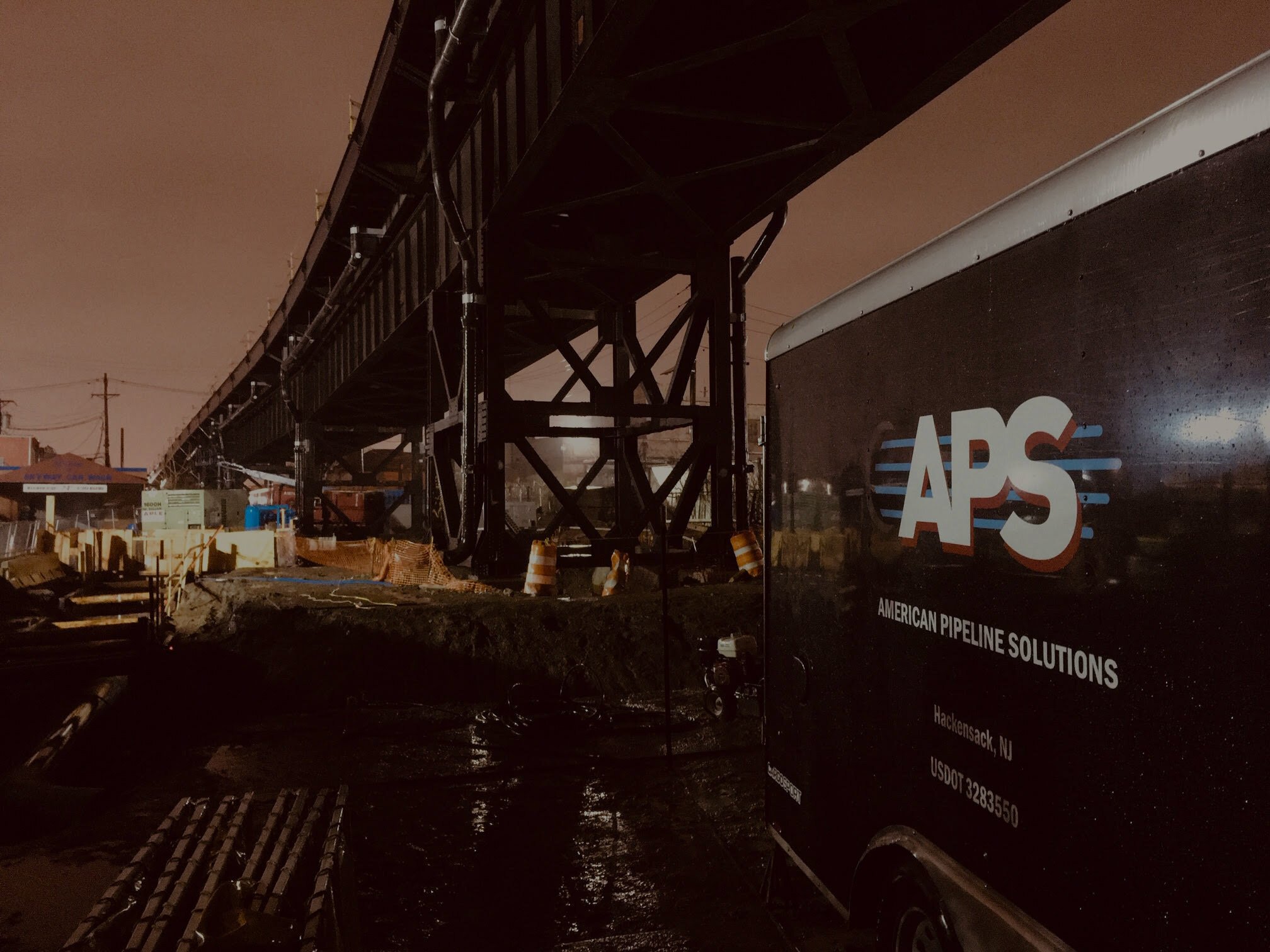
Hydrostatic Testing
Pipeline hydrostatic testing is one of the most popular procedures that can be performed on a pipeline to establish it’s operational fitness. Due to the normally high pressures required for these tests, safety and attention to detail when following industry procedures is of the utmost importance. Hydrostatic testing is necessary to both ensure a pipeline's integrity and to establish it’s MOAP (maximum allowable operating pressure).
Pipeline hydrostatic testing can sometimes be just as much art as science. Understanding the multitude of variables that can affect a test is important. Temperature, elevation, water source, air pockets and inadequate stabilization can all affect pressure and test outcome.
Hydrostatic testing begins after the pipeline has been filled with one of APS’s high flow pumps and is then brought to test pressure with a “squeeze” pump equipped with a stroke counter depending on the required SMYS (specified minimum yield strength).
APS’s Technicians then utilize certified/calibrated deadweights, recorders and digital gauges to monitor and record pipeline pressure over the course of the test. Once the test is complete and the client is satisfied, APS Technicians carefully de-pressurize the line in accordance with industry code and standards.